RESEARCH
ROGUE MANUFACTURES THE WORLD’S MOST DURABLE BARBELLS
This is How We Did It
Rogue spent a decade and over $2,000,000 in scientific testing, research, and development to make our bars more durable than any other bars on the market. We have optimized our materials and manufacturing processes. We also developed a proprietary, patented process we call Rogue Work Hardening™ (RWH). Barbells treated with RWH™ are more resistant to the stresses of being repeatedly dropped. Rogue launched this project because of an unprecedented change in the manner in which barbells are used. The widespread introduction of high repetition Olympic Weightlifting movements resulted in extraordinary increases in the demands placed on bars. Rogue has also developed a clear and meaningful scale for rating barbell durability that makes it easy for you to choose the correct barbell for your application.
Durability Improvements
Rogue’s team of engineers and materials scientists studied the use and abuse that cause the most stress to barbells. They studied alloys and manufacturing processes from across many different industries and developed a plan to make our bars as durable as possible.
The first step was to optimize our steel alloys’ chemical and mechanical properties. Barbells with low tensile and yield strength are more likely to bend with normal use. [1] Tensile and yield strength that is too high can be detrimental, making the metal brittle. [2]
The second step was to rethink barbell coatings. Chrome has been the “gold” standard of barbell plating for many, many years. Rogue’s exhaustive scientific analysis has shown conclusively that chrome decreases the durable lifespan of barbell shafts. Chrome remains an excellent, wear resistant sleeve coating and Rogue will continue to use it for this application.
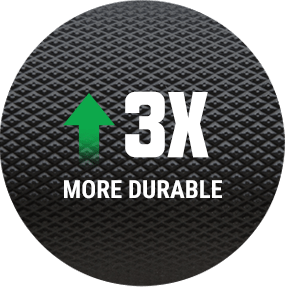
The final step was to find a way to make our barbells resistant to the stresses of being dropped. To this end, Rogue developed the proprietary, patent pending process Rogue Work Hardening (RWH™). Thousands of hours of independent scientific fatigue testing and analysis demonstrate conclusively that Rogue barbell shafts treated with RWH™ have improved durability and last longer than untreated bars when subjected to the stresses of being dropped. Additionally, this process has been shown to keep surface damage from impacting the durable lifespan of the bar.
History of Barbell Use
The Berg Hantel barbell set that was loaned to Bob Hoffman of York Barbell by Henry “Milo” Steinborn in the early 1930’s. York copied the design and every barbell in use today owes its heritage to this barbell. This set is housed at the Rogue campus in Columbus, OH.
Weightlifting has evolved considerably since its early days. When we think of weightlifting we picture bars being dropped from overhead, but dropping weights is a relatively recent development. Rogue looked back to the beginning of modern weightlifting to get a comprehensive view of barbell design and the reasoning behind it. Although weightlifting has been part of the Olympics since the first modern games in 1896, [3] The first adjustable weight, revolving sleeve barbell was not introduced until 1928. These were made by the Berg Hantel company in Germany. [4] By the 1930’s Weightlifting movements were performed using deep dish plates. These were intended to spread out the load and limit damage to the weightlifting platforms when dropped. In competition, lifts were required to be lowered to the ground for safety reasons. Dropping weights was frowned upon for anything other than a failed lift until bumper plates became common in the 1970’s.
Machined 45 lb plates made by Rogue for the Arnold Strongman Classic Deadlift Competition, these were made to match the dimensions of the original deep dish plates that were used in the early days of weightlifting.
Even after bumper plates were introduced, most bars were not dropped. They were used for slow lifts done at gyms such as bench press, squats, curls, overhead press and rows. Only a small percentage of bars were used for powerlifting or Olympic weightlifting.
Dropping the bar during Olympic weightlifting produces far more stress on a barbell shaft than traditional bodybuilding movements and powerlifting movements. It follows then that the bars subjected to the greatest stresses were in Olympic Weightlifting training centers. By examining journals and training diaries of the Olympic Training Center and other high level weightlifting clubs we learned that bars at large facilities were dropped 10,000-20,000 times per year. Some bars were dropped from chest or waist height in powerlifting gyms when performing power cleans or deadlifts. However, as will be detailed later, the increased weights used for these lifts in powerlifting gyms have a protective effect on the shaft when dropped.
Around 2005, high repetition Olympic Weightlifting movements gained popularity and bumper plates became more readily available. From that point on it became common for bars to be dropped up to 150,000 times per year in gyms. This is up to a 15X increase in drops. The number of people using barbells in this manner has grown at a dramatic pace so the number of barbells seeing this type of use has increased commensurately.
Determination of Stresses Placed on a Barbell
Rogue realized that due to these factors we needed to have a complete understanding of the mechanical forces that affect barbells. We contracted the failure analysis engineers at SEA Limited, a world leader in consumer product testing, to quantify the stresses that are placed on a barbell when dropped.
The stresses placed on a barbell were determined by measuring strain. Stress is the loading of a force onto a material and strain is the deformation of that material due to the force. The stress in pounds per square inch (PSI) was calculated from the strain measurements.
Electronic strain gauges were attached to the shaft of a barbell and the bars were dropped from overhead. The electronic signal from the strain gauge was measured and recorded several thousand times per second to obtain an accurate measurement of the stress due to a sudden impact.
Figure 1 shows a representative strain measurement from the shaft of a 28.5 MM barbell loaded to 135 lbs with a single 45 lb bumper plate on each side, dropped from a height of 75”. This height corresponds with an overhead drop by an average height male athlete. The height was measured to the bottom of the bumper plates, the shaft was level and the floor was smooth bare concrete. The impact created a shock wave in the shaft that dampens out over ¼ second.
Figure 1
To evaluate the effect of dropping the barbells at an angle, the same barbell was dropped at approximately 10 degrees off level. A representative strain gauge response for this type of drop is shown in Figure 2.
Figure 2
The effect of different bumper plate material was evaluated by using two 45-pound competition bumpers. Although these have a larger central plate and are narrower than the training bumper plates, there was little difference in the amount of strain recorded. A representative strain gauge response for these drops is shown in figure 3.
Figure 3
The location of the maximum tensile (pulling) stress, at the top of the shaft, indicates that the high stress of the shaft where it meets the sleeves was generated from the reaction of the sleeve impacting the hub of the bumpers as the bumpers impacted on the floor and the end of the sleeve continued to travel downward.
This suggests that reducing the weight loaded on the barbell will not significantly reduce the stress imparted on the shaft. To evaluate this theory, a bar was loaded to 65 lbs with a single 10 lb plate per side and dropped from 75 inches. If the total weight of the loaded barbell was the driving force for the stress, the stress should be much smaller in this case than the when the bar was loaded to 135 lbs. As can be seen in Figure 4, the stress was only 10% lower than the 135 lb drop. If the stress on the bar was proportional to the total weight of the bar, the expected stress would be much lower, 48% (65/135) of the heavier drop.
Figure 4
If the stress is being caused by the unsupported end of the sleeve moving down after the plates hit the ground, increasing the weight to 225 lbs by using two 45 lb weights on each end should not increase the impact stress and may reduce it because location of the force exerted on the sleeve by the bumpers is shifted closer to the center of the sleeve. This was proven to be the case, as is shown in figure 5. This indicates that very high weights that require several bumpers per side create little stress in the shaft when dropped.
Figure 5
If the stress is being caused by the unsupported end of the sleeve moving down after the plates hit the ground, increasing the weight to 225 lbs by using two 45 lb weights on each end should not increase the impact stress and may reduce it because location of the force exerted on the sleeve by the bumpers is shifted closer to the center of the sleeve. This was proven to be the case, as is shown in figure 5. This indicates that very high weights that require several bumpers per side create little stress in the shaft when dropped.
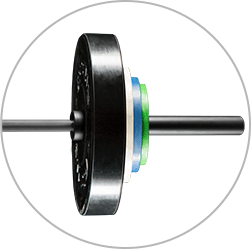
However, if in addition to bumpers, smaller diameter plates that do not impact the ground are used, they greatly increase the bending stress of impact. This weight configuration has been shown to increase the chances of a bar bending when dropped.
To further confirm the role of the sleeves in creating high stresses in the shaft when the barbells are dropped, a trial was conducted placing two 45 lb bumpers in the center of the sleeves instead of against the collars. This test resulted in a significant reduction in the maximum stress in the shaft on impact as shown in Figure 6.
Figure 6
The strain of impact that we recorded is not a smooth curve. As shown in Figure 7, there are small peaks superimposed on the dominant stress wave at 1.14 seconds indicating interference between 2 or more competing stress waves. Figure 6 shows even more irregularity. These competing waves could add or subtract from one another leading higher or lower maximum stress. This situation is most pronounced when one side of the bar hits before the other.
Figure 7
Significance
Testing indicates that stresses as high as 120,000 PSI (0.004 x 30,000,000 PSI) are commonly generated and that stresses as high as 144,000 PSI are possible when the barbells are dropped from overhead. This is confirmation of high level repeated loading, much greater than the stress from a heavy squat, where the change in direction at the bottom of the squat is not nearly as fast as a falling bar being suddenly stopped by the floor.
Because the stress is caused by the unsupported end of the sleeve continuing to move down after the plates hit the ground, reducing the load to the most common weights that are dropped in high repetition Olympic Weightlifting, (65-135 lbs) causes greater stress than dropping heavier weights such as 315 lbs from overhead. Therefore, in a gym that practices high repetition low weight Olympic Weightlifting movements, the highest number of cycles are placed on a barbell at the highest level of stress.
1. High Stress
2. Medium Stress
3. Low Stress
Because the weight of the unsupported ends of the sleeves is what leads to the stress on the shaft, shorter sleeves decrease this stress. Therefore, the shafts of our shorter sleeve barbells such as the Rogue C-70 experience less stress when dropped than standard men’s or women’s barbells.
Laboratory Simulation of the Stress of Dropping a Bar
Once Rogue determined the stresses that are placed on barbells, the engineering team chose a 4 point flexural test (4 point bend test) to simulate this stress in a testing environment. To perform this test the bar is supported at two points and a load is applied in the opposite direction at the mid-span of the two supports by 2 loading pins 2 inches apart. The load is cycled between a small load to keep the bar in place, and a large load to create the desired stress. This test delivers the maximum stress to the entire length of the shaft between the two loading points.
The stress level used for testing was chosen by going slightly above the maximum stress that we observed in drop testing. The maximum stress we observed in a 28.5 MM men’s barbell was in the offset drops, reaching 144,000 psi. Therefore, we chose a test stress level of 150,000 PSI to ensure that we were providing a margin of safety above what a barbell would see in use.
Because the sleeves are what cause the stress in the shaft, the engineering team kept the load the same for all bars with standard men’s sleeves. This includes bars such as the Ohio Bar, the Rogue Olympic WL Bar and the Ohio Power Bar. However, the load was adjusted for women’s bars, and the C-70 Bar to account for the decreased force generated by the shorter sleeve.
Results
One fact that became immediately apparent was that certain coatings significantly decreased the durable lifespan of the bar. For example, chrome which has long been considered to be the “gold” standard for barbell plating, decreased the fatigue life of the shaft by up to 50%. This effect was independent of the manufacturer of the bars, the type of steel and the type of chrome. We tested European chrome bars, U.S. chrome bars and Chinese chrome bars. The results were the same in every case. Chrome reduced the fatigue life of the barbell shafts. Because of problems with chrome, Ivanko Barbell discontinued the use of chrome plating in the 1970’s. [1] The deleterious effect of chromium plating on the fatigue life of steel has long been known in other industries. [5], [6], [7] Other coatings such as zinc and Cerakote did not significantly affect the fatigue life of a barbell shaft.
As expected, diameter had an effect on the fatigue life.
Stress = Force / Area
This means that with the same sleeve, as the diameter and therefore the cross sectional area go up, the amount of stress that the shaft experiences when dropped goes down. While this is an interesting finding, it is not very useful. Athletes should choose the diameter based on what is optimum for their sport, not based on durability. Additionally, while a 25 MM women’s bar is a smaller diameter than men’s bars 28 MM to 29 MM bars, the shorter sleeves cause less stress when dropped. These two factors cancel eachother out leading to durability that is similar to men’s bars.
Another expected finding was that surface damage to the barbell from corrosion or placing it in rack without protective plastic decreased the durable lifespan of the bar.
In the absence of damage, surface preparations for plating such as media blasting were shown to improve the fatigue life of the shafts.
Most importantly, our proprietary process, Rogue Work Hardening™ (RWH™) was shown to significantly increase the fatigue life of barbell shafts when subjected to the stresses of being dropped from overhead. This process has been shown to retain its performance improvement even when subjected to surface damage.
The F Scale™
Choosing the right barbell can be difficult. There is no industry standard for reporting barbell properties. Therefore, you are presented with an array of numbers which vary by manufacturer and very often do not provide useful information. Commonly reported specifications include:
- Tensile Strength – The amount of force that steel can withstand before it fails
- Yield Strength – The amount of force that steel can withstand before it deforms
- Weight ratings such as 1000 lbs or 1500 lbs
While the tensile and the yield strength give information about the strength of the shaft, they can be misleading regarding durability. It is true that bars with low tensile and yield strength are more likely to bend with normal use. [1] This would make you think that the higher the tensile strength, the better. Because of this, there has been an arms race going on between manufacturers for years. Each company has been trying to outdo the others by pushing the tensile strength higher. However, not only have many of the tensile strength claims made by manufacturers been shown to be exaggerated, making the tensile strength as high as possible is not the best strategy. Once the tensile strength reaches 190,000 to 220,000 PSI and the yield reaches 170,000 to 200,000 PSI, bending under normal use is no longer an issue and increasing the tensile and yield strength beyond these levels can be detrimental, making the metal brittle. [2]
The static weight rating, while appearing more practical, does not provide useful information. This rating is determined by loading the bar in a rack until it bends which tells you nothing about how the bar will perform. In use, barbells receive a dynamic stress rather than a static stress. Bars used for Olympic weightlifting movements receive intense dynamic stress during the very fast second pull and exponentially greater stress as they hit the ground when being dropped from overhead after the lift.
By testing finished barbell shafts using the 4 point bend test at a stress level appropriate for the barbell sleeve, we are able to assign a durability rating or F Rating™ to each barbell. Performing the test in this manner accounts for all of the factors that contribute to barbell durability when dropped, Diameter, Tensile Strength, Coating, Sleeve Length, and the presence or lack of media blasting and/or RWH™.
The F Rating of a barbell is directly correlated to the number of cycles the shaft lasted in the 4 Point Bend Test at a stress level appropriate for the type of sleeve used on the bar. For example, a 28 MM chrome plated bar with a tensile strength of 215,000 PSI tested at the stress level for a men’s sleeve that lasted 35,000 cycles in our test received a rating of F1. A shaft, tested in the same manner that lasted 70,000 cycles in our test received a rating of F2. A shaft that lasted 210,000 cycles in our test received a rating of F6.
Media blasting a barbell before coating leads to improved performance on the 4 point bend test. The effects of Rogue Work Hardening™ extend much deeper than media blasting. As a result, this process has been shown to retain its benefits even when confronted with surface damage. Barbells that have been treated with RWH™ are designated by having an R in their F Rating™.
How a bar is used will affect its durable lifespan. As detailed above, dropping a bar from overhead causes more stress on a barbell shaft than traditional bodybuilding or powerlifting movements. Because of this, barbells used for slow lifts will last much longer than the same barbell used for Olympic Weightlifting. Barbells used in commercial facilities will see more volume and therefore more cumulative stress than barbells used by single athletes.
Using this data, we are able to make recommendations on what F Rating is appropriate for different situations.
F1 rated barbells have been used for more than 50 years in Olympic weightlifting training gyms and are an excellent choice for individual athletes, gyms that focus on Olympic weightlifting, and gyms that have dedicated Olympic weightlifting training areas. However, Rogue would not recommend F1 bars as the best choice for large gyms where bars will be dropped repeatedly in low weight Olympic lifts.
F2 and F4 rated barbells have a proven track record of standing up to high level use in facilities performing high repetition, low weight Olympic lifts and other lifts that are dropped from overhead. An F4 rating is achieved by shortening the sleeves of an F2 bar, which reduces the stress on the shaft.
F6-R and F8-R rated bars are engineered for superior resistance to the stresses of dropping and are among the most durable bars available for this application. These barbells are an excellent choice for the owners of the largest facilities where bars will see hundreds of thousands of drops per year.
F12-R and F16-R rated barbells with shorter sleeves (whether in a 28.5mm or 25mm diameter) reduce the stress on the shaft after each drop as compared to a bar with standard length sleeves, creating this elite category of long-term durability. Optimized for high-volume gyms, short-sleeve RWH bars also offer space-efficiency benefits with options for convenient rackability, as well.
F100-R rated bars, which are all stainless steel with RWH, are the most durable bars available and are the best choice for home gyms or large commercial gyms where the owners want the ultimate peace of mind. In addition to their durability, they require little maintenance due to the corrosion resistance provided by their stainless steel construction.
Conclusion
Rogue has created an industry standard for the durability rating of barbells. The big winner with this scale is customer. Rather than relying on a meaningless static strength rating or trying to make sense of tensile and yield strength, you can know how durable your bar is compared to other bars on the market.
Our hope is that the F Scale will expand beyond Rogue and allow customers use F Ratings when choosing the bar for their application regardless of the manufacturer.
Rogue openly invites any brand to bring your engineers and barbell steel with plating variants to Columbus, Ohio. We will open up the lab and let you test your bars. We only ask that you are honest with your customers when you see the results. Once we test your steel, we will add it to the data we have collected to better refine the F Rating.
We have tested most of the barbell competitors from around the globe. Simple things we know from this testing annually thru February of 2024:
- Chrome is not good for barbell durability
- 28MM for high repetition gyms such as CrossFit affiliates is a poor design choice. Coupling this with chrome is even worse. Painting the bar orange does not impact strength or durability!
- US Sourced steel barbell manufacturers are more durable as of February 2024. Barbells tested from China consistently test low on durability
- Rogue Stainless Barbells with RWH are the most durable barbells on the planet
If you would like to test your barbell, please email us at bartesting@roguefitness.com
Thank you,
Bill Henniger
Reference
- Lincir, Tom. “Ivanko.” Articles | Ivanko – Official Website of Ivanko Barbell Company, Ivanko Barbell Company, 2018, www.ivankobarbell.com/press/.
- Pang, J.c., et al. “General Relation between Tensile Strength and Fatigue Strength of Metallic Materials.” Materials Science and Engineering: A, vol. 564, 2013, pp. 331–341., doi:10.1016/j.msea.2012.11.103.
- “About.” International Weightlifting Federation, International Weightlifting Federation, www.iwf.net/focus-on-iwf/about/.
- Todd, Jan. “https://www.rogueaustralia.com.au/theindex/article/from-milo-to-milo-a-history-of-barbells-dumbells-and-indian-clubs-iron-game-history-april-1995”. Iron Game History, vol. 3, no. 6, Apr. 1995, pp. 4–16., doi:10.18411/d-2016-154
- Logan, Hugh L. “Effect of Chromium Plating on the Endurance Limit of Steels Used in Aircraft.” Journal of Research of the National Bureau of Standards, vol. 43, no. 2, 1949, p. 101., doi:10.6028/jres.043.012.
- Williams, C., and R. A. F. Hammond. “The Effect of Chromium Plating on the Fatigue Strength of Steel.” Transactions of the IMF, vol. 32, no. 1, 1954, pp. 85–106., doi:10.1080/00202967.1954.11869670.
- Stepurenko, V. T., et al. “Effect of Electrolytic Chromium Plating Quality on Fatigue Strength of Steel.” Soviet Materials Science, vol. 8, no. 4, 1974, pp. 398–401., doi:10.1007/bf00728753.